Construction professionals are taking a different tone for mass timber. The last several years brought it into the mainstream, but perhaps it was too quick. Mass timber boasted shorter timelines and heightened eco-awareness while championing other sector hurdles. In time, oversights and flaws seeped through warped and cracking wood.
Will contractors dismiss mass timber, or will innovators mend its shortcomings? Discover what mass timber’s advent taught experts about the industry’s future.
Environmental Impact and Sustainability
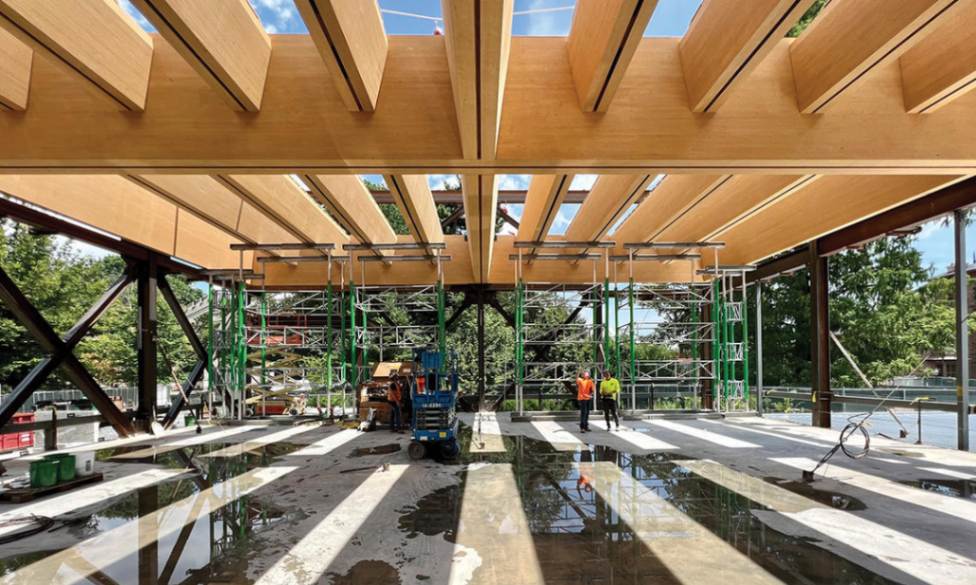
Source – paw.princeton
A London workplace consisting of spruce, walnut and beech was a product of mass timber. It is a carbon-neutral feat, using 80% fewer transport demands than comparable concrete buildings. Trucks produced fewer tailpipe emissions and waste as a result. Reviewing construction’s carbon emissions reveals wood is less intensive than alternatives. So, how could wins like this flip in light of the sector’s popularity?
The primary argument for mass timber is its carbon sequestration potential. It is a logical leap to assume decarbonizing urbanization only requires wood infrastructure. However, more forests are at risk of deforestation as this method increases in popularity. Thorough oversight and management are necessary for mass timber to be a mainstay.
Organizations like the Forest Stewardship Council certify ethical forestry operations, but builders are not required to seek regions with its stamp of approval. Construction companies do not always source sustainable wood or dispose of it responsibly at the end of its life cycle. Some even take timber from overseas, exacerbating carbon footprints from excess transportation needs. Damaged, rotting timber releases sequestered carbon, diminishing its green contribution.
Structural Integrity and Durability
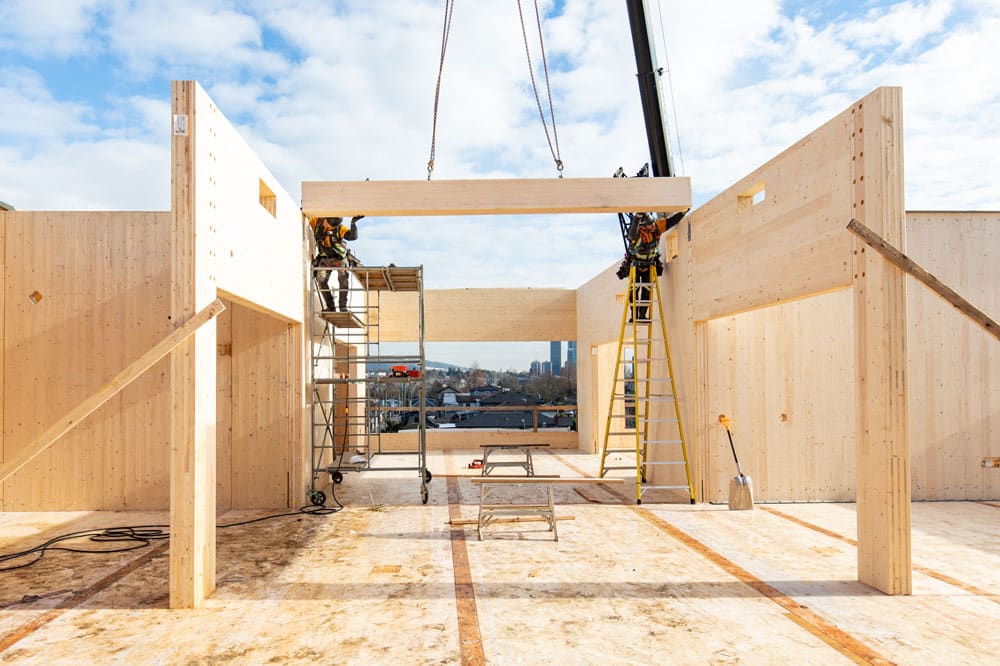
Source – naturallywood
Widespread adoption of new materials is questionable in any business. Short-term gains cannot predict long-term defects, which may occur en masse. Claims suggest mass timber has a powerful strength-to-weight ratio, more so than steel.
It becomes more robust with timber frame joints. These steel elements reduce the chances of decay and foundational sagging while increasing aesthetics. This does not eliminate the possibility of buildings succumbing to flooding, termites or seismic activity.
The detractors forced insurance providers to design mass timber-curated offerings. Standard building insurances were not enough. This is an indicator that the market will want premiums for using these builds because their dependability is up for debate. Some plans also review the dangers of transporting beams to work sites. The industry understands traffic disruptions and closures are likely because of them.
These buildings must be as easy to take apart as they are to put together. It is a delicate balancing act to consider mass timber’s degradation potential to optimize for streamlined replacements. Simultaneously, everything needs strong adherence, which would make retrofits more challenging. It allows contractors to replace mass timber building components as if they were modular. However, this malleability may compromise long-term integrity.
Cost Considerations
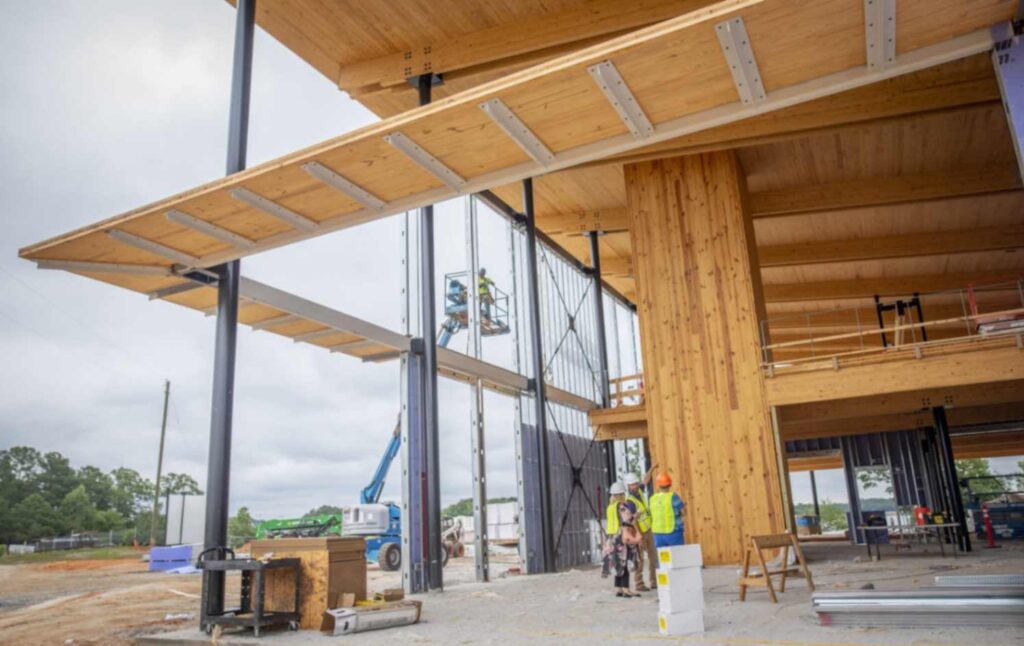
Source – images.squarespace-cdn
Prefabrication is at the heart of mass timber. Most construction agencies work on-site, reacting to the elements as nature happens. Unexpected and unwelcome influences may cost stick-built structures a fortune. Torrential storms and delays in material transport add up. Forging buildings in environmentally controlled factories sounds like relief from financial headaches.
The upfront costs of mass timber implementation are worth noting, as popularity causes erratic market values. Acquiring and building out production equipment may be more feasible than other costly materials, like steel and concrete.
Corporations may also onboard new staff with mass timber expertise, increasing expenses. Consultants, timber fabricators and engineers with prefab experience promise savings. But, it may be a while before they feel the return on investment is worth it.
Profits may fluctuate during transitions, too. Demand for mass timber is skyrocketing, leading to supply chain disruptions. Labor shortages compound this concern. Therefore, builders relying on mass timber’s advantages may wait to bank on them immediately, skewing the worthiness of adopting it in the first place.
Regulatory Challenges and Building Codes
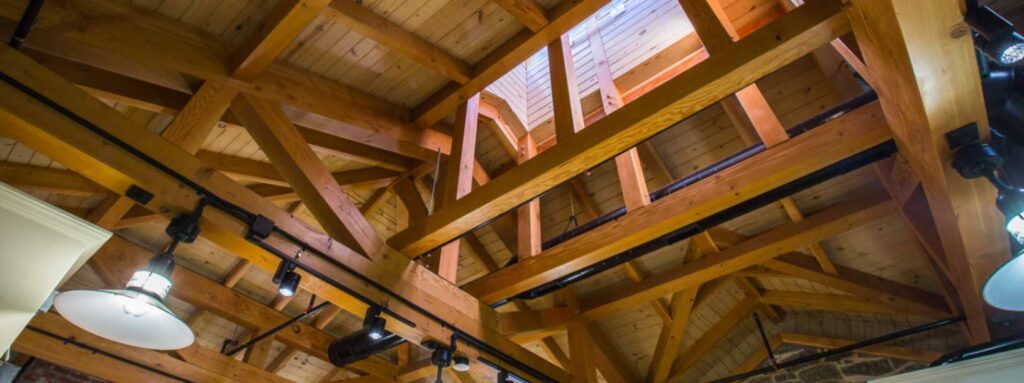
Source – matfllc
Mass timber’s value may be $1.5 billion by 2031 after garnering international attention. However, most market growth remains in Europe. The EU wants net-zero buildings by 2050, and mass timber promises eco-friendly materials. So, the nation is the most proficient and familiar with mass timber’s nuances.
This implies areas outside the EU may have limited building codes for guidance. The 2021 International Building Code expanded what builders can construct with mass timber. They can be residential or commercial, up to 18 stories. However, countries need regulators to draft region-specific guidelines. The structure will not have essential components for sustainability and stability if it does not consider regional weather and ecosystems.
Developing comprehensive documentation is time-consuming in addition to manufacturing overhauls. Earning mass timber’s perceived benefits may not be globally accessible because of this.
The planning process for a prefab build is more extensive than conventional operations. The intent is to erect buildings quickly, leaving little room for contractors to stray from work orders. Designing compliant processes with designers, plumbers and subcontractors in mind requires intricate standards. Evaluating the moving parts’ requirements for inefficiencies takes time.
Fire Safety Concerns
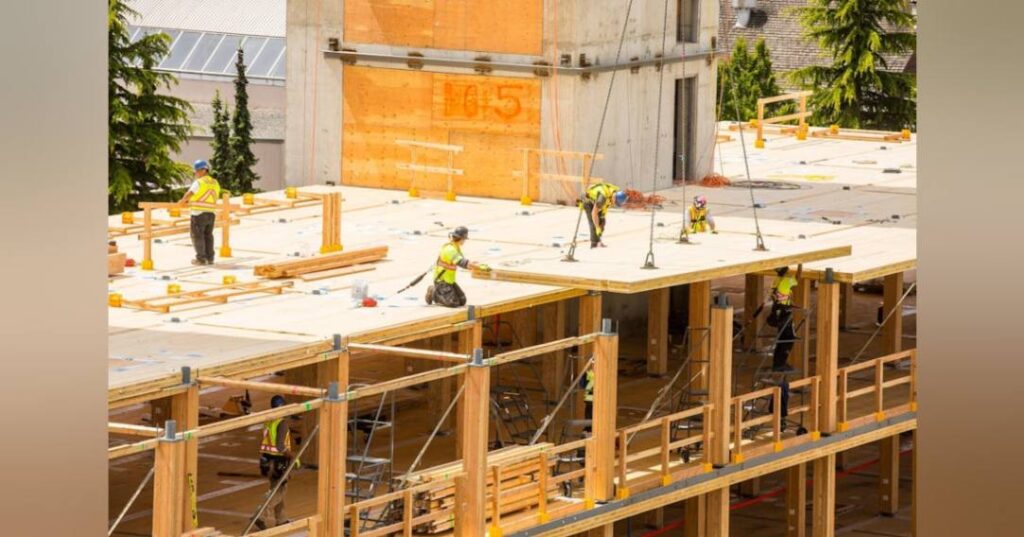
Source – img.firehouse
Timber buildings are evolving into skyscrapers as new codes permit more stories. Contractors assemble buildings with steel and advanced adhesives to resist flames. Fire prevention is a priority for salvaging mass timber’s reputation, but how effective are modern measures? These are typically safe dwellings, but that does not mean incidents are unheard of.
Manufacturers rely on treatments to shield timber from fires. Intumescent coatings stave off high temperatures, delaying the wood from catching. The reaction forms a char to make flames burn slower. However, places like New York City realized relying on them is not foolproof. Using them on products like structural composite lumber is insufficient to achieve a fire-resistance rating.
A notable apartment fire alerted the sector of other red flags in fire safety. The incident resulted in 72 preventable deaths in a mass timber building. It passed fire safety tests, and the wood was not responsible. Other elements — like an aluminum composite and plastic — were the causes for the blaze. Experts may be too focused on perfecting the fire resistance of timber without reinforcing the rest.
Is This the End of Mass Timber?
Several negative realizations about mass timber are not enough to dismantle it, but experts are more aware of its shortcomings after all the initial hype. Innovators view strategies with a more critical eye, discovering opportunities for improvements.
Businesses leveraging mass timber must use their improved awareness to make changes. Enthusiastic collaboration is vital for it to be the sustainable, productive answer to construction’s woes.